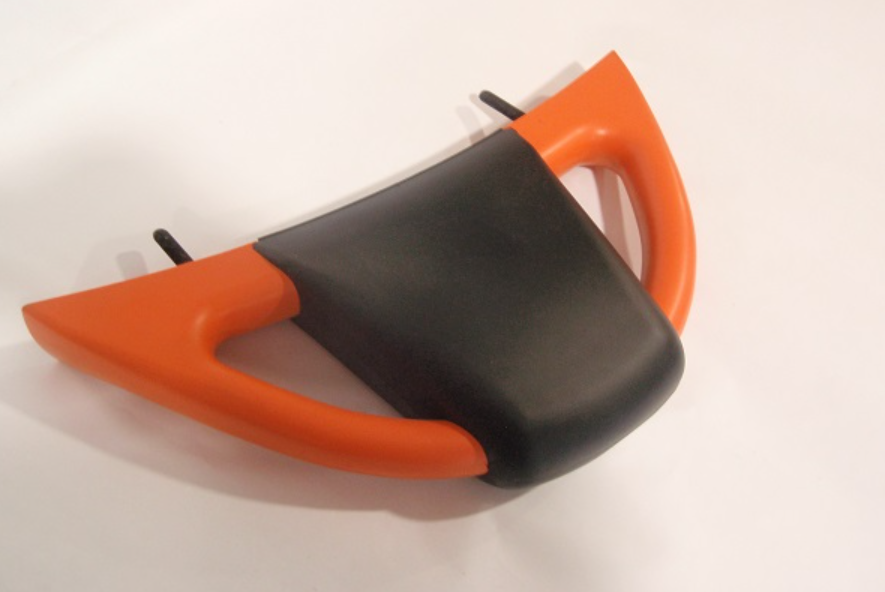
Polyurethane Foam Moulding: A New Era in Custom Foam Solutions
Introduction: The Innovation of Foam Moulding
Foam moulding, particularly foam moulding, has revolutionized how industries design and manufacture soft yet durable components. From ergonomic vehicle parts to acoustic insulation, polyurethane foam offers unparalleled versatility. Among the leaders in this field is Acoustafoam, a company with over 36 years of experience delivering bespoke foam solutions tailored to various industries’ needs.
This article explores the process, applications, and advantages of foam moulding, focusing on integral skin polyurethane moulding, while shedding light on its growing role in sectors like automotive, marine, construction, and more.
1. Understanding Polyurethane Foam Moulding
At its core, polyurethane foam moulding involves mixing two components that undergo a chemical reaction, producing a flexible yet durable foam. When poured into custom-designed moulds, the material forms a finished product after curing and trimming. The result is a lightweight, resilient object with a tough outer skin and a microcellular inner core.
This skin, known as integral skin, is formed during the moulding process and can be chemically textured to resemble materials like leather. The hardness of these moulded components can range from 30 to 90 Shore A, offering tailored durability for different applications.
Key Features:
- Tear-resistant surface
- Flexible core
- UV stability
- Customizable textures and colors
- Fire retardant and acoustic options
2. Benefits of Polyurethane Foam Moulding
Businesses across the globe are turning to foam moulding for its unique advantages. Here’s why:
a. Durability Meets Comfort
Integral skin foam offers a rare combination of softness and strength, making it perfect for items that require a comfortable grip or cushioned support—such as armrests or headrests.
b. Versatile Applications
From steering wheels and gear knobs to marine safety products, moulded polyurethane foam can be found in virtually every sector.
c. Custom Engineering
Foam moulding allows for metal inserts, color matching, texturing, and shaping to exact specifications. Whether the need is for high-precision or low-volume parts, Acoustafoam’s expertise makes it possible.
d. Sound and Thermal Benefits
Used in acoustic barriers and thermal insulation, polyurethane foam provides enhanced environmental control inside vehicles, buildings, and boats.
e. Eco-Conscious Manufacturing
Many foam moulding processes are moving toward CFC & HCFC-free formulations, making them safer for the environment and compliant with global standards.
3. Applications Across Industries
Polyurethane foam moulding is not limited to one sector. Its applications span numerous industries:
Automotive
Foam moulded components such as grab handles, seating, fascia panels, and gear knobs are essential in enhancing vehicle interiors. Acoustafoam supplies first and second-tier components, combining performance with design flexibility.
Marine
Engine rooms and cabins in yachts and boats benefit from polyurethane foam for both acoustic insulation and thermal management, often using Class 0 foam for fire resistance.
Construction & Heavy Machinery
Foam moulded solutions like radiator sound barriers, seat cushions, and trims help reduce noise and vibration, crucial for operator comfort and workplace safety.
Furniture & Office Equipment
Office chairs, armrests, and back supports all use foam moulding to offer ergonomic comfort and durability.
Gaming & Medical
Joystick grips, gaming pads, and orthopaedic supports utilize moulded polyurethane for tactile precision and long-term usability.
See also: Why Are Businesses Turning to AI for Biometric Solutions?
4. Beyond Moulding: Foam Conversion Solutions
Acoustafoam doesn’t stop at moulding. Their foam conversion capabilities extend into precision engineering for customized foam products. Using advanced equipment like CNC profiling machines, water jets, and die-cut presses, they can cut, shape, and assemble foam for even the most complex needs.
From acoustic insulation panels to engine room thermal shields, their foam conversion services include:
- Cutting (die, water jet, CNC)
- Laminating
- Spray coatings
- Custom fabrication
These services are tailored to various foam types such as polyurethane, polyethylene, and polystyrene, ensuring that clients get the most suitable solution for their product or environment.
5. Acoustic and Thermal Management: A Critical Role
Acoustic foam and acoustic barriers made from polyurethane foam are used to reduce sound transmission and vibration. Products like C03, C09, and C024 polymeric barriers are particularly effective for:
- Automotive engine blocks
- HVAC systems
- Industrial machinery
- White goods and home appliances
- Military and medical equipment
Combined with foam moulding, these materials offer dual benefits of form and function—protecting components while minimizing noise pollution.
6. Commitment to Quality and Innovation
What sets Acoustafoam apart is not just their technical know-how but their commitment to innovation and quality. Their approach includes:
- CAD-assisted design
- Fast prototyping
- In-mould coating for added durability
- UV-stable painting for weather resistance
- Fire-retardant options
- Rigid material insert compatibility
Whether your project requires low, medium, or high-volume runs, Acoustafoam uses tooling made from resin, aluminium, or steel, matched to production requirements and budget.
7. Sectors Served by Acoustafoam
With decades of experience, Acoustafoam caters to an expansive list of sectors, including:
- Automotive
- Marine & Boats
- Public Transport & Rail
- Military Vehicles
- HVAC
- Power Generation
- Domestic Goods
- Construction Equipment
- Material Handling
- Medical and Healthcare
- Industrial Acoustics
- Machinery Enclosures
Each sector presents unique challenges, and Acoustafoam meets them with bespoke polyurethane foam solutions that are tested, refined, and trusted.
Conclusion: Shaping the Future with Foam Moulding
Foam moulding, especially using polyurethane foam, represents a frontier of possibilities for industries seeking durability, comfort, and customization. Through its combination of technical expertise, state-of-the-art tooling, and customer-focused innovation, Acoustafoam continues to lead the charge in delivering tailor-made solutions that meet rigorous performance standards.
From grab handles and acoustic panels to marine insulation and medical supports, polyurethane foam moulding has transformed from a manufacturing method into an engineering solution that shapes the products of tomorrow.